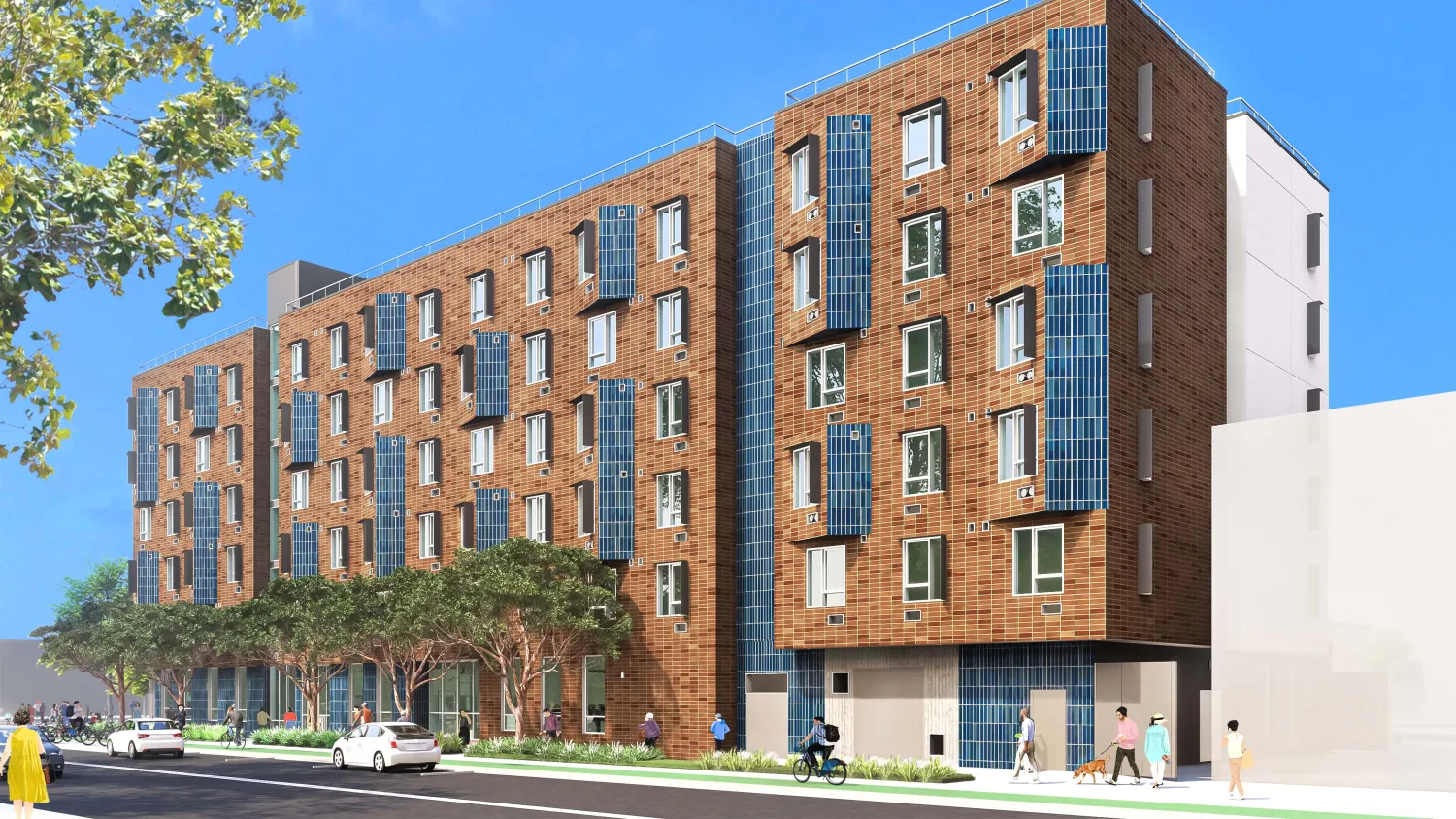
In late 2023, construction crews demolishing an empty warehouse at 1633 Valencia St. uncovered a century-old, hand-painted ad for the “Chevrolet Six,” a “ghost sign” that became the talk of the neighborhood in San Francisco’s Mission-Bernal enclave.
Now the property is getting attention for another reason: It’s the site of a new six-story, affordable-housing building that has quickly shot up.
“I hear from a lot of people who live and work around there who are shocked at how quickly it went up,” said Clare Murphy, a project manager with nonprofit developer Mercy Housing.
Just eight months after breaking ground, the 146-unit senior project has installed its roof and windows, and crews are waterproofing it. The first residents are expected to move in late this year.
“It’s been somewhat of a breeze,” Murphy said.
For the team behind 1633 Valencia — Mercy Housing, the San Francisco Housing Accelerator Fund, David Baker Architects and Cahill Contractors — the project is the latest test of how to speed up and cut costs for affordable housing in famously expensive San Francisco.
The project uses the same floor plan and efficient design of Mercy’s earlier affordable project, 833 Bryant St., and only contains studios. It also uses the so-called “design build” approach where the entire team — developer, general contractor, architect and sub-contractors — is assembled at the start of the planning process.
“If you get everybody in the process early on you can figure out how to do things less expensively and more rapidly without losing quality or value,” Baker said. “There is a lot of inefficiency within the typical delivery process in San Francisco.”
Jacqueline Hemenway, a project manager with Cahill, agreed, explaining that the permitting process is streamlined in this model.
“It’s bringing the team on early but also a team that has worked together before,” she said.
The approach succeeded at 833 Bryant St., which was built for $423,000 per unit, including the cost of land, roughly 40% cheaper and faster than comparable projects, according to a study by the Urban Institute.
So far, the Valencia project is coming in at about $540,000 a unit, not including the cost of land, which adjusted for inflation is similar to the Bryant Street project. The 19-month construction schedule is three to six months faster than comparable projects. The project is about 20% cheaper than comparable studio projects and about 40% less than some affordable developments.
However the 833 Bryant project, dubbed The Tahanan, was attacked by construction unions who criticized that it was largely built off-site at a modular factory in Vallejo, which means less work for the city’s construction workers.
In the four years since opening, the building has been the source of 29 complaints of mold, leaks, poor insulation, power outages and broken elevators — prompting San Francisco Building and Trades Council President Larry Mazzola to say “you get what you pay for.”
Although it’s unclear to what extent the modular construction is to blame for the flaws, at 1633 Valencia St. the development team sought to meet cost and speed goals comparable to Tahanan but avoid the political baggage by not using modular construction.
While it is not a modular project, 1633 Valencia is using some pre-fabricated components — the floors, ceilings and staircases are built off-site at facilities in Oregon and Susanville (Lassen County) and trucked to San Francisco.
Housing Accelerator Fund Executive Director Rebecca Foster said the goal at 1633 Valencia has been to “replicate the savings we achieved at Tahanan but demonstrate there are a variety of ways to do it.”
The off-site fabricators follow the detailed 3D modeling provided by the design and construction teams, which “takes months off the project,” said Baker.
The Housing Accelerator Fund’s innovation fund is also backing projects in Santa Cruz and Santa Clara. The nonprofit raised $50 million from Sobrato Philanthropies, Destination: Home and Apple.
The project is also likely to receive an unusual level of scrutiny because Tipping Point, the nonprofit founded by Mayor Daniel Lurie, was a partner in the 833 Bryant St. project.
Baker said the development is being “run more like a typical market-rate project,” where design build is more common.
“Market-rate developers build for less because they are more flexible,” said Baker.
Mercy Housing got involved in the Valencia Street project by invitation of Sequoia Living, which is planning to build a seven-story affordable senior complex at 3485 Cesar Chavez St. next door. The taller, 126-unit project is expected to start construction in 2026. The two projects will share a large interior courtyard.
Project architect Won Young Kim of David Baker Architects said the construction process has been “much smoother” than it was at 833 Bryant St.
The fact that so many details are ironed out early in the design build process saves money. Those funds can then be used to help with leasing the building.
“If they are going to bust their butts to bring down cost and time on construction, allowing them to reallocate some portion of those savings makes sense and will make residents’ life better,” said Foster.
While the project has not received the same union opposition as did 833 Bryant, Rudy Gonzalez, secretary-treasurer of the San Francisco Building Trades Council, said he was not thrilled that much of the carpentry is being done off-site.
He said that the union supports off-site prefabrication of construction components in San Francisco for use in the city. For example, components are being assembled in Mission Bay for use at the Helen Diller UCSF medical campus under construction at the Parnassus campus.
“I can’t guarantee they are paying proper prevailing wages for jobs,” he said. “Every hour we lose to an out-of-area contractor, whether it is prefab or for onsite, is an hour of work that a local San Franciscan doesn’t get.”
But given the urgency of creating homes for thousands of homeless people, time is of the essence, said Foster.
“The reason we have to do it so much faster and cheaper is because we know every additional week that someone is unhoused, the acuity of their needs increases dramatically,” said Foster.
View the full article: This S.F. affordable housing project is building faster and cheaper apartments. Here’s how, which appeared in the San Francisco Chronicle on February 22, 2025.